Plazma se pro svoji vysokou teplotu a výbornou elektrickou vodivost používá v průmyslu a v dílnách na efektivní dělení (řezání) materiálů. Jak ale funguje řezání plazmou a na jaké materiály ji můžeme použít? Jaké výhody a nevýhody přináší využití plazmy? Umíme ovlivňovat kvalitu a rychlost plazmového řezání?
Plazma je vysoce ionizovaný plyn
Celosvětově používaný název plazma vzešel od amerického fyzika Irvinga Langmuira před přibližně 100 roky. Plazma je ionizovaný plyn složený z nabitých iontů a záporných elektronů, proto je vysoce vodivý. Ionizace plynu se dosahuje jeho ohřevem na vysokou teplotu nebo pomocí elektrického výboje mezi elektrodami. Tehdy se elektrická energie změní na tepelnou, aby mohla vzniknout plazma. Je to čtvrté skupenství hmoty (první tři si pamatujeme ze ZŠ :)). Na naší planetě ji v přirozené podobě známe jako plamen ohně, ve formě blesku nebo polární záře. V okolním vesmíru však má téměř absolutní zastoupení, vzhledem k tomu, že všechny hvězdy jsou v podstatě plazmatické koule. Pro vysokou teplotu a vodivost si našla množství uplatnění i v technice.
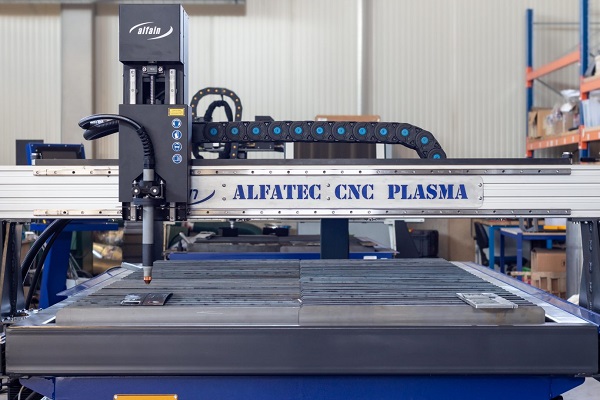
Výhody plazmového řezání
Plazmové řezání nabízí zjevné výhody, kvůli kterým se čím dál více uplatňuje nejen v průmyslu, ale i v dílnách:
- vysoká rychlost řezání – vyšší produktivita, v porovnaní s řezáním kyslíkem je plazmové řezání mnohem rychlejší (až 5x),
- jednoduché ovládání řezačky,
- řezání všech kovových materiálů, i vysoce legovaných a barevných kovů, díky vysoké teplotě v pracovní oblasti,
- řezání různých geometrických tvarů,
- relativně malé tepelné ovlivnění materiálu,
- mobilita ruční řezačky,
- u ručního řezání se nepoužívají žádné speciální plyny – používá se stlačený vzduch, což zvyšuje také bezpečnost (nepoužívají se hořlavé plyny),
- na manuální plazmové řezání není třeba vysoká kvalifikace.
Nevýhody řezání plazmou
- nižší kvalita povrchu řezu,
- omezená hloubka řezu – běžně do 30 mm, pro silnější materiály je řezání plazmou neekonomické. U strojních CNC řezaček se proto kombinuje technologie řezání plazmou např. s řezáním plamenem, které umožňuje hlubší řezy.
- větší šířka řezné spáry – dosahuje až několik milimetrů,
- vyšší hlučnost – roste se zvyšováním intenzity proudu,
- při průmyslovém použití mají CNC plazmy relativně nižší svislou rovnoměrnost řezu,
- odsávání spalin odsávacími a filtrovacími zařízeními u průmyslových řezaček.
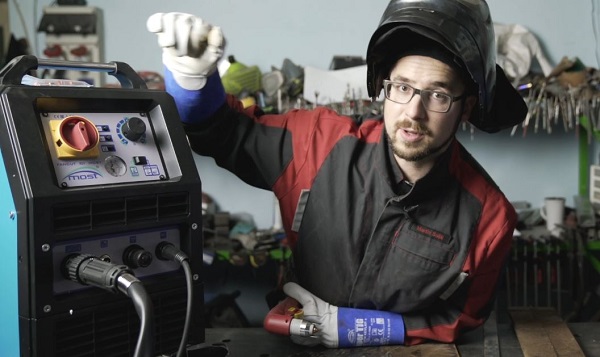
Jaké materiály se dají řezat plazmovým paprskem?
Plazma se používá především k řezání kovů (vodivých materiálů). Podobným způsobem je však možné dělit s ní i nevodivé materiály, k čemuž se ale používá jiný princip vytvoření plazmového oblouku, který je popsán níže.
Plazmové řezání můžeme tedy použít pro:
- všechny vodivé materiály:
- konstrukční ocel, měkkou, uhlíkovou, nerezovou i legovanou ocel,
- hliník, měď, mosaz, slitiny, titan, mangan...
- nevodivé materiály – plast, keramiku.
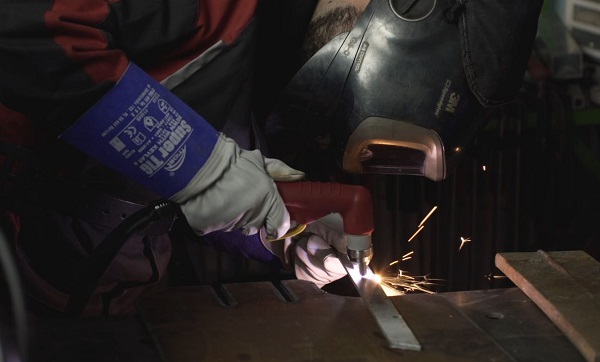
Princip plazmového řezání
Plazmové řezání materiálů probíhá pomocí vysokoteplotního plazmového oblouku. Proces řezání vodivých a nevodivých materiálů je podobný, ale způsob vzniku plazmového oblouku je rozdílný.
Vodivé materiály jako ocel nebo hliník se řežou tak, že plazmový oblouk vzniká mezi plazmovým hořákem a obráběným kovovým materiálem. Inertní plazmový plyn (stlačený vzduch) je hnaný vysokou rychlostí do úzké trysky v hořáku. Vysoké napětí mezi netavící se wolframovou elektrodou a tryskou vytvoří elektrický oblouk, který ionizuje proudící plyn. Tento oblouk se nazývá pilotní netransferovaný oblouk. Část z plazmového plynu se přemění na plazmu a přenese se (přeskočí) na obráběný materiál. Tak se už vytvoří plazmový elektrický oblouk mezi elektrodou, která je katodou (–) a vodivým povrchem obráběného materiálu, který tvoří anodu (+). Pilotní oblouk se vypíná, mezi elektrodou a materiálem už hoří plazmový oblouk (řezací, transferovaný oblouk) vysoké teploty, který roztaví materiál. Přebytečný roztavený materiál je odfukován plazmovým plynem s vysokou průtokovou rychlostí, čímž vzniká řezná mezera.
Teplota oblouku může dosáhnout až 33 000 °C a rychlost proudu částic 1 500 až 2 300 m/s. Plazmový oblouk je stabilizovaný (po výstupu z trysky je třeba ho udržet ve tvaru tenkého paprsku) a chráněný vůči atmosféře ochranným plynem nebo vodou (průmyslové řezačky). Stabilizační médium zároveň chladí hořák i řezaný materiál.
Nevodivé materiály jako plasty a keramika se řežou pomocí plazmového oblouku, který je vytvořený v hořáku mezi výstupní tryskou (většinou měděnou) a wolframovou elektrodou. Jelikož nejsou tyto materiály vodivé, nemohou s elektrodou hořáku vytvořit elektrický obvod. Ten musí probíhat výlučně v plazmovém hořáku. U tohoto způsobu řezání je tryska intenzivně namáhaná, a proto se rychle opotřebovává. Tento princip je známý jako netransferovaný oblouk a je použitelný i pro vodivé materiály.
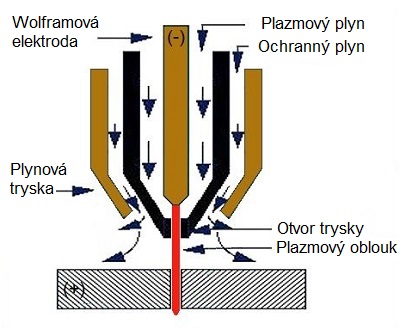
Co ovlivňuje rychlost a kvalitu řezu plazmou?
Efektivitu a kvalitu plazmového řezání je možné ovlivnit kombinováním parametrů (chce to trošku zkušeností a experimentování, jako u všeho):
- výkon zdroje, napájecí proud a napětí – pro tenčí materiály použijeme nižší výkon, abychom materiál zbytečně po krajích neroztavili, řez by byl nerovný,
- tloušťka a druh řezaného materiálu – u silnějších materiálů klesá rychlost řezání,
- průměr trysky – pro získání co nejvyšší teploty je třeba velmi malý průměr otvoru trysky,
- vzdálenost plazmového hořáku od materiálu – u menší vzdálenosti se zvyšuje kvalita řezu; pro udržení konstantní vzdálenosti slouží tzv. vozík (vodítko) na plazmový hořák,
- plazmové plyny a jejich čistota – plyny vysoké čistoty zvyšují rychlost řezání.
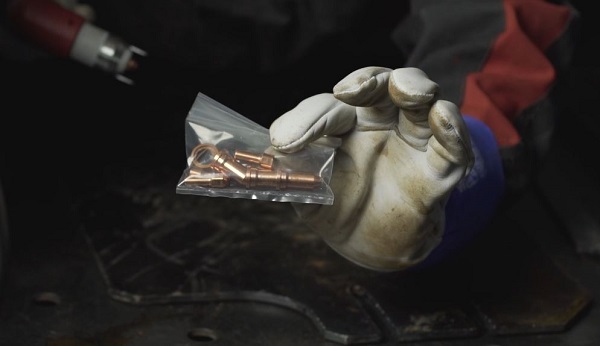
Kompresor plazmové řezačky a plyny na řezání plazmou
Pro ruční plazmové řezání se jako plyn používá stlačený vzduch. K vhánění vzduchu využívá ruční plazmová řezačka většinou kompresor, který je buď zabudovaný přímo v řezačce nebo je nejčastěji samostatným zařízením. Takový kompresor musí splňovat požadavky podle pokynů výrobce plazmové řezačky, kde je přesně definován maximální tlak vzduchu, plnicí množství, chlazení, filtr, odlučovač oleje a kondenzátu a podobně.
Průmyslové plazmové řezací stroje někdy používají kromě vzduchu i inertní plyny. Důvodem je zlepšení vlastností, například při řezání neželezných kovových materiálů.
- plazmové plyny – přivádějí se přímo do elektrického oblouku a následně jsou ionizované: argon, helium, dusík N2, kyslík O2, oxid uhličitý CO2, směs Ar+H2, filtrovaný vzduch,
- ochranné plyny – chrání paprsek plazmy a oblast taveného materiálu před nepříznivými účinky atmosféry: argon, dusík N2, směs O2 + N2, Ar + H2, Ar + N2, filtrovaný vzduch,
- fokusační plyny – jsou málo používané, zužují, zaostřují paprsek plazmy, který vystupuje z trysky: argon, směs Ar + H2, Ar + N2.
Výběr plynu záleží na tloušťce materiálu, žádané kvalitě řezu, použitého plazmového zdroje a hořáku, i na nákladech na plyn.
Plazmové řezání na jednoduché a rychlé dělení kovů
Řezání plazmovým paprskem je rychlý a jednoduchý proces dělení kovových vodivých materiálů do tloušťky cca 30 cm. Je efektivnější, než řezání plamenem, ale má omezenou tloušťku řezání. Na druhé straně můžeme porovnávat laserové řezání, které je zase nepoměrně dražší. Díky efektivitě, možnosti řezat komplikované tvary s poměrně malým tepelným ovlivněním materiálu se z čistě průmyslového využití řezání plazmou rozšířilo i do dílen. V dílnách se samozřejmě nepoužívají velké CNC průmyslové stroje, ale malé, přenosné řezačky, o kterých se více dozvíte v článku Ruční plazmová řezačka – jak si ji vybrat a používat.